Influence of Seawater Absorption on the Hardness of Glass Fiber/Polyester Composite
DOI:
https://doi.org/10.57159/gadl.jcmm.1.1.22003Keywords:
Degradation, Hydrolysis, Polyester composites, Hardness, Material chemistryAbstract
In the marine industry, glass fibers are commonly used to reinforce polyesters for ship hulls, submarine components, and other marine structures. Isophthalic polyesters are a feasible alternative due to their superior mechanical qualities and added end-of-life scenarios compared to orthophthalic polyesters. However, like other fiber composite systems, glass fiber reinforced polymer (GFRP) composites are also water sensitive. Here, GFRP composites of three different thicknesses are aged under three different immersion periods in seawater (20, 40 and 60 days). All samples are reconditioned and evaluated for hardness following aging. Significant emphasis is placed on the presence of calcium carbonate, over which increases in moisture content irrevocably reduce the composite’s hardness. Compared to untreated material, the hardness of 6, 8, and 10 mm composites decreased by 25.64, 10.92, and 4.63% after the 60-day aging period. This drop is mostly the result of microstructure evolution manifesting as an increase in porosity. Consequently, fiber deterioration, fiber cracks, and degradation of polymer-fiber bonding emerge in the composite, decreasing hardness.
References
Rubino, F., Nisticò, A., Tucci, F., & Carlone, P. (2020). Marine Application of Fiber Reinforced Composites: A Review. Journal of Marine Science and Engineering, 8, 26.
Horsmon, A. W. (1994). Composites for Large Ships. Journal of Ship Production, 10(4), 274-280.
Selvaraju, S., & Ilaiyavel, S. (2011). Applications of composites in the marine industry. Journal of Engineering, II(II), 89-91.
Siriruk, A., & Penumadu, D. (2014). Degradation in fatigue behavior of carbon fiber–vinyl ester based composites due to sea environment. Composites Part B: Engineering, 61, 94-98.
Sen, R. (2003). Durability of advanced composites in a marine environment. International Journal of Materials and Product Technology, 19(1/2), 118.
Gu, H. (2009). Dynamic mechanical analysis of the seawater treated glass/polyester composites. Materials & Design, 30, 2774-2777.
Gu, H. (2009). Behaviours of glass fibre/unsaturated polyester composites under seawater environment. Materials & Design, 30, 1337-1340.
Kootsookos, A., & Mouritz, A. (2004). Seawater durability of glass- and carbon-polymer composites. Composites Science and Technology, 64, 1503-1511.
Mayya, H. B., Pai, D., Kini, V. M., & N. H, P. (2021). Effect of Marine Environmental Conditions on Physical and Mechanical Properties of Fiber-Reinforced Composites—A Review. Journal of The Institution of Engineers (India): Series C, 102, 843-849.
Smith, P. (2007). Metallic Materials for Piping Components. In The Fundamentals of Piping Design (Chapter 3, pp. 115-136). Houston: Elsevier.
Patel, G. C. M., Chate, G. R., Parappagoudar, M. B., & Gupta, K. (2020). Optimization of Machining of Hard Material. In SpringerBriefs in Applied Sciences and Technology (pp. 103-128).
Anand, P. B., Lakshmikanthan, A., Gowdru Chandrashekarappa, M. P., Selvan, C. P., Pimenov, D. Y., & Giasin, K. (2022). Experimental Investigation of Effect of Fiber Length on Mechanical, Wear, and Morphological Behavior of Silane-Treated Pineapple Leaf Fiber Reinforced Polymer Composites. Fibers, 10, 56.
Neale, M. (Ed.). (1995). Hardness. In Tribology Handbook (Chapter 3, p. E3.1). Elsevier (2nd ed.).
Rawat, S., & Attia, H. (2009). Wear mechanisms and tool life management of WC–Co drills during dry high-speed drilling of woven carbon fiber composites. Wear, 267, 1022-1030.
Subramanian, K., & Cook, N. H. (1977). Sensing of Drill Wear and Prediction of Drill Life. Journal of Engineering for Industry, 99, 295-301.
Geng, D., Liu, Y., Shao, Z., Lu, Z., Cai, J., Li, X., Jiang, X., & Zhang, D. (2019). Delamination formation, evaluation, and suppression during drilling of composite laminates: A review. Composite Structures, 216, 168-186.
Tsao, C., & Hocheng, H. (2007). Effect of tool wear on delamination in drilling composite materials. International Journal of Mechanical Sciences, 49, 983-988.
Bhat, R., Mohan, N., Sharma, S., Kini, A. U., Shivakumar, S., & Naik, N. (2020). Multi-response parametric optimization in machining of marine application-based GFRP composite with HSS drill: Application of TOPSIS approach. Materials Today: Proceedings, 28, 2077-2083.
Ullah, I., Wasif, M., Tufail, M., Khan, M. A., & Iqbal, S. A. (2019). Experimental Investigation of Cutting Parameters Effects on the Surface Roughness and Tools Wear during the Drilling of Fiber Reinforced Composite Materials. Mehran University Research Journal of Engineering and Technology, 38, 717-728.
Aich, U., Behera, R. R., & Banerjee, S. (2019). Modeling of delamination in drilling of glass fiber-reinforced polyester composite by support vector machine tuned by particle swarm optimization. International Journal of Plastics Technology, 23, 77-91.
Bora, C., Bharali, P., Baglari, S., Dolui, S. K., & Konwar, B. K. (2013). Strong and conductive reduced graphene oxide/polyester resin composite films with improved mechanical strength, thermal stability, and antibacterial activity. Composites Science and Technology, 87, 1-7.
Akter, R., Sultana, R., Alam, Z., Qadir, R., Begum, M., & Gafur, A. (2013). Fabrication and Characterization of Woven Natural Fibre Reinforced Unsaturated Polyester Resin Composites. International Journal of Engineering & Technology IJET-IJENS, 13(2), 122-127.
Elkington, M., Bloom, D., Ward, C., Chatzimichali, A., & Potter, K. (2015). Hand layup: understanding the manual process. Advanced Manufacturing: Polymer & Composites Science, 1, 2055035915Y.000.
Arumugam, C., Arumugam, S., & Muthusamy, S. (2020). Mechanical, thermal, and morphological properties of unsaturated polyester/chemically treated woven kenaf fiber/AgNPs@PVA hybrid nanobiocomposites for automotive applications. Journal of Materials Research and Technology, 9, 15298-15312.
Hall, W., & Javanbakht, Z. (2021). How to Make a Composite—Wet Layup. In Advanced Structured Materials (Vol. 158, pp. 33-53).
Xin, J. H., Zhang, Y., Huang, Q., & Cheng, N. Y. (2019). The research about ultimate load of CFRP repaired pipes under long-term seawater immersion and bending moment. IOP Conference Series: Materials Science and Engineering, 634, 012028.
Singh, M. K., & Zafar, S. (2021). Wettability, absorption, and degradation behavior of microwave-assisted compression molded kenaf/HDPE composite tank under various environments. Polymer Degradation and Stability, 185, 109500.
Wang, G., Huang, D., Ji, J., Völker, C., & Wurm, F. R. (2021). Seawater-Degradable Polymers—Fighting the Marine Plastic Pollution. Advanced Science, 8, 2001121.
Starkova, O., Gaidukovs, S., Platnieks, O., Barkane, A., Garkusina, K., Palitis, E., & Grase, L. (2021). Water absorption and hydrothermal aging of epoxy adhesives reinforced with amino-functionalized graphene oxide nanoparticles. Polymer Degradation and Stability, 191, 109670.
Das, D., Pradhan, S. K., Nayak, R. K., Nanda, B. K., & Routara, B. C. (2020). Influence of curing time on properties of CFRP composites: A case study. Materials Today: Proceedings, 26, 344-349.
Pandya, A., Upadhaya, P., Lohakare, S., Srivastava, T., Mhatre, S., Pulakkat, S., & Patravale, V. B. (2022). Nanobiomaterials for regenerative medicine. In Nanotechnology in Medicine and Biology (Chapter 6, pp. 141-187). Elsevier.
Karayannidis, G. P., Chatziavgoustis, A. P., & Achilias, D. S. (2002). Poly(ethylene terephthalate) recycling and recovery of pure terephthalic acid by alkaline hydrolysis. Advances in Polymer Technology, 21(4), 250-259.
Chawla, K. K. (2012). Composite Materials. New York, NY: Springer New York (3rd ed.).
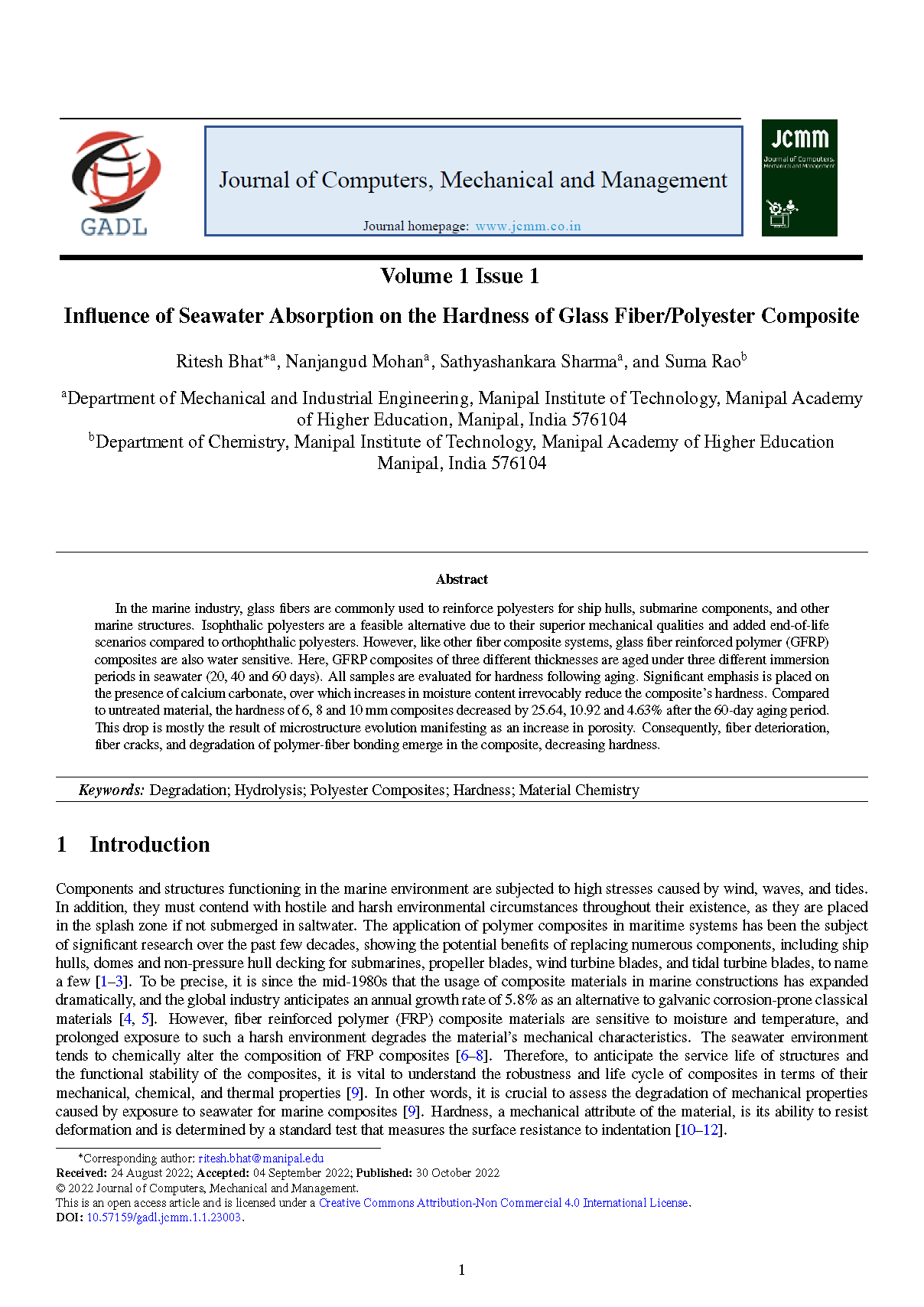
Downloads
Published
How to Cite
Issue
Section
License
Copyright (c) 2022 Journal of Computers, Mechanical and Management

This work is licensed under a Creative Commons Attribution-NonCommercial 4.0 International License.
The Journal of Computers, Mechanical and Management applies the CC Attribution- Non-Commercial 4.0 International License to its published articles. While retaining copyright ownership of the content, the journal permits activities such as downloading, reusing, reprinting, modifying, distributing, and copying of the articles, as long as the original authors and source are appropriately cited. Proper attribution is ensured by citing the original publication.