Experimental Analysis of Machining Parameters In Turning of Aluminum 7075
DOI:
https://doi.org/10.57159/gadl.jcmm.2.3.23061Keywords:
High-Speed Machining, Aluminum 7075, Process Parameters, Response Surface Methodology, OptimizationAbstract
High-Speed Machining (HSM) of aluminum alloys represents a critical area in manufacturing industries, including automotive, aerospace and consumer electronics. This research presents an in-depth investigation into the effects of key process parameters on the HSM of Aluminum 7075, a high-strength alloy with superior mechanical properties. Utilizing the central composite design of Response Surface Methodology (RSM), the study scrutinizes the impact of process parameters, including cutting speed, feed, depth of cut and tool nose radius on surface roughness. The findings reveal feed and nose radius as primary factors influencing surface roughness while cutting speed and depth of cut play secondary roles. This comprehensive analysis contributes to the knowledge base for efficient machining practices and lays the groundwork for future optimization strategies. It also underscores the necessity for further research into understanding the intricate dynamics of machining parameters to enhance operational efficiency and product quality in the machining of Aluminum 7075 and similar alloys.
References
H. Reinecke, C. M¨uller, and S. Karazi, “Micromachining,” in Reference Module in Materials Science and Materials Engineering, Elsevier, 2016.
F. Yang, K. Gao, I. W. Simon, Y. Zhu, and R. Su, “Decomposition methods for manufacturing system scheduling: a survey,” IEEE/CAA Journal of Automatica Sinica, vol. 5, pp. 389–400, mar 2018.
V. P. Astakhov, “Turning,” in Modern Machining Technology, pp. 1–78, Elsevier, 2011.
W. A. Knight and G. Boothroyd, Fundamentals of Metal Machining and Machine Tools. CRC Press, aug 2019.
S. Mok, “Aluminum Economy for Sustainable Development: Aluminium as Core Material for Energy Storage and Energy Saving Products: Low Cost, High Performance, and Easy Processing in Developing Countries,” in 2011 IEEE Global Humanitarian Technology Conference, pp. 21–24, IEEE, oct 2011.
D. Flom, “High-Speed Machining of Metals,” Annual Review of Materials Research, vol. 14, pp. 231–278, jan 1984.
Z. Q. Liu, Y. Wan, and X. Ai, “Recent Developments in Tool Materials for High Speed Machining,” Materials Science Forum, vol. 471-472, pp. 438–442, dec 2004.
T. Ranjan Soren, R. Kumar, I. Panigrahi, A. Kumar Sahoo, A. Panda, and R. Kumar Das, “Machinability behavior of Aluminium Alloys: A Brief Study,” Materials Today: Proceedings, vol. 18, pp. 5069–5075, 2019.
N. H. Ononiwu, E. T. Akinlabi, and C. G. Ozoegwu, “Optimization techniques applied to machinability studies for turning aluminium metal matrix composites: A literature review,” Materials Today: Proceedings, vol. 44, pp. 1124–1129, 2021.
D. Dudzinski, A. Devillez, A. Moufki, D. Larrouqu`ere, V. Zerrouki, and J. Vigneau, “A review of developments towards dry and high speed machining of Inconel 718 alloy,” International Journal of Machine Tools and Manufacture, vol. 44, pp. 439–456, mar 2004.
S. C. Cagan and B. B. Buldum, “Variants of high speed machining,” in High Speed Machining, pp. 283–302, Elsevier, 2020.
B. Wang, Z. Liu, Q. Song, Y. Wan, and X. Ren, “A Modified Johnson–Cook Constitutive Model and Its Application to High Speed Machining of 7050-T7451 Aluminum Alloy,” Journal of Manufacturing Science and Engineering, vol. 141, jan 2019.
R. A. Mali, M. D. Agrahari, and T. Gupta, “FE based simulation and experimental validation of forces in dry turning of aluminium 7075,” Materials Today: Proceedings, vol. 27, pp. 2319–2323, 2020.
M. A. A. bin Abdullah, M. A. Muhammad, Z. Ibrahim, M. Y. Ali, and J. Purbolaksono, “Investigation of the turning parameters on the surface finish of an aluminum bar,” in AIP Conference Proceedings, vol. 2643, p. 050001, 2023.
R. Abedinzadeh, E. Norouzi, and D. Toghraie, “Study on machining characteristics of SiC–Al2O3 reinforced aluminum hybrid nanocomposite in conventional and laser-assisted turning,” Ceramics International, vol. 48, pp. 29205–29216, oct 2022.
A. Aswal, A. Jha, A. Tiwari, and Y. Modi, “CNC Turning Parameter Optimization for Surface Roughness of Aluminium-2014 Alloy Using Taguchi Methodology,” Journal Europ´een des Syst`emes Automatis´es, vol. 52, pp. 387–390, oct 2019.
A. Abdallah, “Optimization of cutting parameters for surface roughness in CNC turning machining with aluminum alloy 6061 material,” IOSR Journal of Engineering, vol. 4, pp. 01–10, oct 2014.
T. Sasimurugan and K. Palanikumar, “Analysis of the Machining Characteristics on Surface Roughness of a Hybrid Aluminium Metal Matrix Composite (Al6061-SiC-Al2O3),” Journal of Minerals and Materials Characterization and Engineering, vol. 10, no. 13, pp. 1213–1224, 2011.
A. M. Pinar, “Optimization of Process Parameters with Minimum Surface Roughness in the Pocket Machining of AA5083 Aluminum Alloy via Taguchi Method,” Arabian Journal for Science and Engineering, vol. 38, pp. 705–714, mar 2013.
S. T. Prashantha Kumara, H. P. Thirtha Prasada, N. M, and C. Siddaraju, “Investigate the effect of al2o3 & cuo nano cutting fluids under mql technique in turning of dss-2205,” Advances in Materials and Processing Technologies, vol. 8, pp. 3297–3330, Jul 2022.
A. Samaila, R. Sankar, and A. I. Haruna, “Performance evaluation of mixture of groundnut oil and camel milk as cutting fluids on the surface of aluminium during turning,” Materials Today: Proceedings, jun 2023.
M. Szyma´nski, D. Przestacki, and P. Szyma´nski, “Tool Wear and Surface Roughness in Turning of Metal Matrix Composite Built of Al2O3 Sinter Saturated by Aluminum Alloy in Vacuum Condition,” Materials, vol. 15, p. 8375, nov 2022.
S. H. Musavi, M. Sepehrikia, B. Davoodi, and S. A. Niknam, “Performance analysis of developed micro-textured cutting tool in machining aluminum alloy 7075-T6: assessment of tool wear and surface roughness,” The International Journal of Advanced Manufacturing Technology, vol. 119, pp. 3343–3362, mar 2022.
G. Struzikiewicz and A. Sioma, “Evaluation of Surface Roughness and Defect Formation after The Machining of Sintered Aluminum Alloy AlSi10Mg,” Materials, vol. 13, p. 1662, apr 2020.
S. D. B. Menachery, N. T. and N. Senthilkumar, “Processing of nanoreinforced aluminium hybrid metal matrix composites and the effect of post-heat treatment: a review,” Applied Nanoscience, vol. 13, pp. 4075–4099, jun 2023.
M. Imran and A. A. Khan, “Characterization of Al-7075 metal matrix composites: a review,” Journal of Materials Research and Technology, vol. 8, pp. 3347–3356, may 2019.
M. N. Akhtar, T. Sathish, V. Mohanavel, A. Afzal, K. Arul, M. Ravichandran, I. A. Rahim, S. Alhady, E. A. Bakar, and B. Saleh, “Optimization of process parameters in cnc turning of aluminum 7075 alloy using l27 array-based taguchi method,” Materials, vol. 14, no. 16, p. 4470, 2021.
B. Veluchamy, N. Karthikeyan, B. R. Krishnan, and C. M. Sundaram, “Surface roughness accuracy prediction in turning of Al 7075 by adaptive neuro-fuzzy inference system,” Materials Today: Proceedings, vol. 37, pp. 1356–1358, 2021.
M. Lakshmanan, J. S. Rajadurai, and S. Rajakarunakaran, “Machining studies of al7075 in cnc turning using grey relational analysis,” Materials Today: Proceedings, vol. 39, pp. 1625–1628, 2021.
B. Zhou, B. Liu, and S. Zhang, “The advancement of 7xxx series aluminum alloys for aircraft structures: A review,” Metals, vol. 11, p. 718, Apr 2021.
C. Jawalkar and S. Kant, “A Review on use of Aluminium Alloys in Aircraft Components,” i-manager’s Journal on Material Science, vol. 3, pp. 33–38, dec 2015.
E. Starke and J. Staley, “Application of modern aluminum alloys to aircraft,” Progress in Aerospace Sciences, vol. 32, no. 2-3, pp. 131–172, 1996.
D. Ashkenazi, “How aluminum changed the world: A metallurgical revolution through technological and cultural perspectives,” Technological Forecasting and Social Change, vol. 143, pp. 101–113, jun 2019.
P. G. Petropoulos, “The effect of feed rate and of tool nose radius on the roughness of oblique finish turned surfaces,” Wear, vol. 23, no. 3, pp. 299–310, 1973.
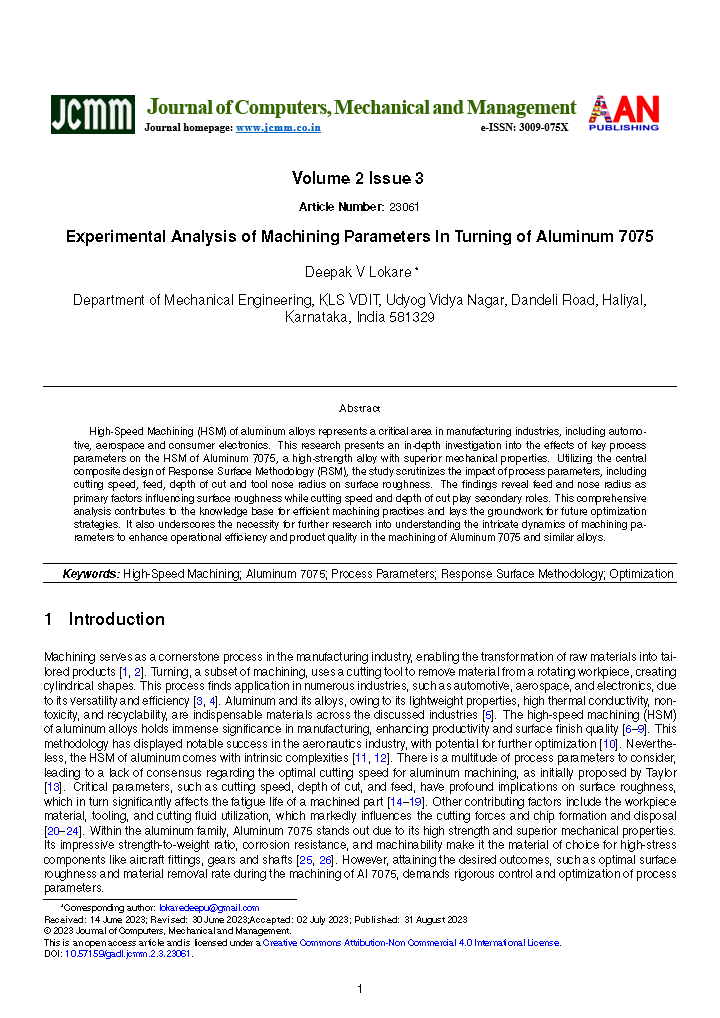
Downloads
Published
How to Cite
Issue
Section
License
Copyright (c) 2023 Journal of Computers, Mechanical and Management

This work is licensed under a Creative Commons Attribution-NonCommercial 4.0 International License.
The Journal of Computers, Mechanical and Management applies the CC Attribution- Non-Commercial 4.0 International License to its published articles. While retaining copyright ownership of the content, the journal permits activities such as downloading, reusing, reprinting, modifying, distributing, and copying of the articles, as long as the original authors and source are appropriately cited. Proper attribution is ensured by citing the original publication.